GVL for the floor: the pros and cons
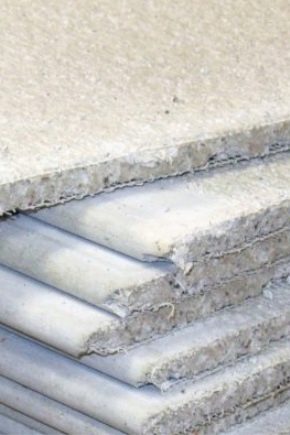
Leveling the floor is one of the most important tasks in the repair. This will ultimately depend on how long this floor will last, how the furniture placed on its surface will be visually perceived, and in general what impression the interior will produce.
It is desirable to achieve alignment so that it is simple, fast and at no extra cost. In order for the leveling layer to serve for a long time, ensure safety and meet the high performance characteristics, you need to be wisely choosing the necessary building material. When installing the flooring, you can use gypsum-fiber sheet - GVL.
Special features
At its core, GVL is a “close relative” of drywall.The structure of the sheets includes gypsum, cellulose, which binds it securely, and other "additives" that ensure the strength of the material and its moisture resistance. It differs from gypsum plasterboard in that it does not have a cardboard casing, its structure is uniform, and it is denser.
In gypsum sheets, there are a number of undeniable advantages:
- Under the floor, which is leveled using this material, you can immediately mount any heating system.
- This coating is lightweight. It is easy to transport and convenient to lay even on not very strong grounds.
- You can do the installation in the winter, since the work does not use materials containing moisture.
- A person without a specific builder’s experience may be engaged in assembling GVL. It is enough to be able to hold tools in hand.
- GLV-floor mounted quickly. In the process of work there is no excess garbage and noise. For laying, on average, it takes no more than one or two days.
- From the traditional materials for leveling the floor - chipboard (chipboard) and DSP (cement-bonded chipboard) - differs in that it does not creak after installation. Does not change shape after a significant change in temperature.
- Well maintains the increased mechanical influences and blows.
- In case of fire, it will become an obstacle on the way of fire. This material does not burn, but only charms.
- There are no restrictions on the use. Gypsum fiber is appropriate in any buildings - low-rise and high-rise.
- Does not emit harmful substances, and therefore is considered safe in terms of ecology.
- By cons GVL can be attributed little.
- It is better to work together with the laying of this material together, since it is inconvenient to handle it alone.
- In case of improper handling of GVL sheet can be accidentally broken.
- The material has a significant cost.
- Variety GVL - moisture-resistant gypsum-fiber sheets (GVLV), although intended for use in rooms with high humidity, can still be affected by rot. On the rotted areas they become soft. Sometimes the sheets have to be replaced entirely.
Kinds
In appearance GVL is a plate or sheet of rectangular shape. Unlike conventional plates, GVLV are treated with special hydrophobic substances. This makes it possible to apply them in the bathrooms and in the kitchens.
Sheets of gypsum fiber are also available, which are glued together and mutually displaced. On the edges they have folds, allowing you to quickly and easily mount the leveling layer of the floor.
Specifications
A typical GVL panel for rooms with a humidity level that does not exceed the norm can have dimensions: length 2500 mm, width 1200 mm, thickness - 10 or 12.5 mm. Moisture resistant plate can be exactly the same format. And it may have smaller dimensions, it is produced in the form of a 1200 square by 1200 mm with a thickness of 10 mm.
In addition, GVLV sheets with dimensions of 1200 by 600 mm, thickness of 20 mm and folds of 50 mm are sold.
For leveling the floor, you can choose slabs with dimensions of 1500 by 1000 mm with a thickness of 10 mm.
The advantage of GVL is that this material has a viscous structure. Therefore, when mounted in capable hands, it does not crumble or crack. It has a low thermal conductivity, in connection with this floor not only levels, but also makes it warm, which is extremely valuable for housing and public buildings.
Due to the fact that it is non-combustible material, it is used to protect building structures from fire.
Gypsum fiber is resistant to frequent and sudden temperature changes. Therefore, in unheated rooms such as garages, country houses, it can be used safely.
Scope of use
GVL panels can be “put into service” to create a dry floor screed in any house. For example, the weight of the bulk screed is about three hundred kilograms per square meter. For its devices have to purchase materials such as cement, gravel, sand, and more. Plus, you must wait until such a screed dries.
Therefore, the use of gypsum-fiber sheet is a great alternative to all these concerns and difficulties.
In addition, not everyone will dare to drag a concrete mixer to upgrade a concrete floor to the upper floor of an apartment building, and it will be difficult to place it in an apartment. Everything is much easier with gypsum fiber and other components necessary for dry screed.
With the help of GVL, you can make a rough floor and above the ceiling of concreteand over the old wooden floors. Wait after the completion of this work is not necessary. You can immediately begin to create the top decorative layer. The laminate flooring, carpet, linoleum and parquet flooring fit perfectly on the GVL, it is possible to put ceramic tile in the bathroom on the GVLV. A gypsum fiber at the same time, among other things, will serve as a sound-insulating layer.
GVL does not contradict the installation of water and electric floor. At the same time it will be enough to use sheets with a thickness of only 10-12 mm. There is no need to worry that the leveling layer will skew, spoiling the entire coverage.
Together with the GVL slabs, fibrous, polystyrene foam and backfill insulators are used to create the insulation layer. Rock wool is a mineral wool of different composition. Styrofoam is similar to ordinary foam. It keeps warm well and is durable. But at the same time it is rather expensive and can ignite.
Filling heat insulators - crushed stone, slag pumice, expanded clay - are not so reliable, but they are much cheaper.
Installation
The hands can make laying gypsum fiber both on concrete and on wooden floor.
First you need to make a calculation on the amount of material needed, purchase it and deliver to the place of installation.
An edge band is installed on a concrete base around the perimeter of the room.
Vapor barrier is performed using plastic film. Put it overlap, so that one lane came to the other about thirty centimeters. The film is fixed with adhesive tape, connecting into a coherent whole.
If any communications or wires pass through the floor, they need to be isolated.by placing in a protective corrugation. Then filling is made with expanded clay, which is leveled. At the same time between the cables and GVL should be at least two centimeters of expanded clay.
Expanded clay fall asleep, focusing on the pre-installed lighthouses. To align the insulating layer is applied long rail.
In the course of tamping the heat insulator, you need to carefully consider the places near the walls, in the corners and at the door.
To make it easier to fill the clay, and in the future and install the plates GVL themselves, you can make guides from a wooden bar. They serve as a guideline, which shows the level to which you need to fill the insulation, and also act as a crate for the fastener GVL.
Gypsum fiber is laid from the angle closest to the doorway. Elements of the subfloor attached glue composition. It may be just PVA or special glue. On the base you can put two layers of gypsum fiber. This will help strengthen the structure. The top layer is placed in the opposite direction to the previous one.The plates are also bonded to each other with glue and fixed with screws.
In the process of work, the surplus of glue, which acts in the joints of the plates and near the walls, must be carefully removed. If the upper decorative coating is subsequently carpeted or laminate, the joints will have to be puttied.
At the end of the ground floor. The primer in the hardware store should be chosen with such an account that it can be combined in its properties with the adhesive composition that was used to connect the HLV-plates to each other.
If we are talking about the improvement of wooden floors, the procedure will be approximately the same as when working with concrete floors, but first you need to attend to the thorough preparation of the base for the GFL.
.
First of all, you should understand the condition of the old floor. It will be necessary to remove the boards and carefully assess the condition of the part that is not visible in the normal situation.
It is possible that it will be necessary to strengthen the design with additional lags. It depends on what kind of flooring material you plan to use as a finishing material.
Just as in the first case, you need to make an alignment.Sometimes this requires lagging. You may have to work with a plane, and in some places, in order to raise the floors, install wedges, or even make props of bricks. Heads of nails and screws on the boards need to be deepened, ensuring that there are no small protrusions that in the future will not allow to accurately form a decorative floor covering.
Check how level the floor is with a level. The remaining flaws must be removed with a sander. Although the plane is also suitable. Small irregularities of the type of cracks are sealed with a putty. If there are deep depressions, sometimes they are enough to fill the fines with expanded clay.
According to the technology of mounting on a wooden base, you need to lay a vapor-permeable material — pgamin or waxed paper.
The skewing of GVL in the course of operation will be hampered by an insulating tape ten millimeters thick and ten centimeters high, laid along the perimeter of the room. Its application to a certain extent will provide sound insulation. The tape itself is made of polystyrene or mineral wool. After the installation of rough floors, the surplus is removed.
To properly lay the plates themselves, you need to mark them with regard to the installed insulation tape. Excess material is cut, putting it on a flat surface, so that it is convenient to cut. For accurate trimming, you will need a hacksaw or a construction knife, as well as round cutters for making shaped holes.
Laying GVL occurs here also with the use of glue. When performing a dry screed, it is enough to glue the sheets together in the area of the folds, on which the adhesive composition is applied. In addition, the plate should be fixed with screws. They are screwed around the perimeter of each panel so that the caps go deeper into the surface by two to three millimeters. On large plates, fasteners occur every thirty centimeters, and on small ones - in twenty.
In the process of laying you need to ensure that the joints of the plates themselves do not fall on the joints of the elements below the layer
It is better to lay the GVL at an angle of 45 degrees relative to the plank floor. Plates should also be shifted relative to each other from row to row.
Tips
Starting installation of GVL-coating, you need to keep in mind a number of nuances.
- After purchasing gypsum fiber, carefully read the instructions for laying it on the floor.
- The gypsum-fiber sheets themselves after their purchase should be stored in a room with low humidity. Do not immediately begin to create a subfloor after the importation of material into the room. Let him stand in him for a few hours.
- If we are talking about leveling a wooden floor with the help of GLS plates, it is better to drill holes in it. This simple technique will not allow the boards to rot further, since the holes will ensure good ventilation.
- Squeaky and wobbling floorboards need to be securely fastened to the logs with screws, which are used in carpentry work.
- When constructing a vapor barrier, the layers of the film must be positioned so that they slightly rise onto the walls, forming a kind of waterproof container on the floor.
- When working with backfilling it is necessary to wear a respirator.
- In the event that a “warm floor” is installed, another layer of insulation will have to be laid under the GVL. These are polystyrene foam plates that will not allow heat to “leak” through the floor.
- GVL double-layer plates are stacked in the same way as single-layer ones, connecting with glue in folded joints.At the walls folds cut. You can use for this and a hacksaw, and jigsaw.
- If the bulk layer under the gypsum fiber is more than ten centimeters, you can lay the sheets in three layers. For the top use the largest plate size.
- The distance between the gypsum-fiber sheets when laying should be no more than two millimeters.
- In rooms with high humidity and where leakage is possible, experts recommend waterproofing in the joints of the gypsum plasterboard, as well as at the junctions of the walls and floors.
- In addition to processing the attachment points for self-tapping screws and joints on gypsum fiber gypsum plaster putty, it is recommended to lay a reinforcing tape on top and press it in.
Finishing can be started just a day after laying gypsum-fiber sheets.
How does the installation of gypsum-fiber sheets over the base of the floor with expanded clay, see the following video.