Non-flammable insulation: how to choose a safe insulation?
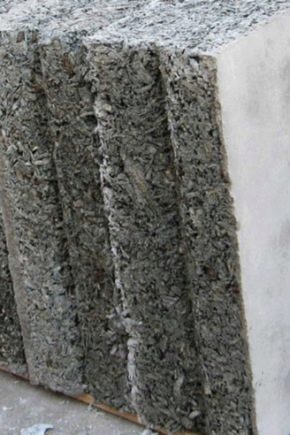
Nonflammable insulation is very popular, due to the wide scope of its application. What are the types of non-combustible insulation? What material to use for a specific construction task? This will be discussed in our article.
Special features
Non-combustible material for thermal insulation must comply with the following characteristics:
- burning with a visible flame is possible, but its duration does not exceed 10 seconds (that is, the insulation may catch fire, but a fire with an open flame lasts no more than the specified time);
- at the moment of burning, the temperature of the insulating material does not rise above 50 ° C;
- during burning the heater cannot lose more than 50% of the weight and volume.
Types and properties
Insulation may have a different basis and production technology, which determines its appearance and technical characteristics. Consider the main types of non-combustible insulating material.
Loose
They are stones and formations of various factions, which are poured into the space of a building structure. As a rule, for greater thermal efficiency, it is recommended to use loose insulators of various dimensions: the larger ones provide thermal insulation, small ones fill the space between them.
The following materials belong to loose types of nonflammable heaters.
- Expanded clay. Environmentally friendly material, based on clay. Suitable for thermal insulation hard to reach places. In addition to high thermal insulation characteristics, it has moisture resistance. Expanded clay is the best suited for the isolation of fire-hazardous objects, it has long been used in the organization of industrial furnaces.
- Expanded vermiculite. The product is based on hydromica subjected to high-temperature roasting. Usually with the use of this material is carried out insulation of low-rise buildings, as well as attic space and external insulation. Differs in environmental friendliness and the improved indicators of biostability, from lacks - inability to resist to influence of moisture. Level it allows only high-quality and properly mounted waterproofing.
- Perlite. A material based on volcanic glass that provides low thermal conductivity and low weight. Only 30 mm of perlite can replace 150 mm of brick masonry in terms of its thermal efficiency. Among the shortcomings - low moisture resistance.
Cellular
Externally, these heaters look like frozen soap suds. The most common fire-resistant cellular insulating material is foam glass. It is produced by sintering glass chips with coal or another gasifier. It is characterized by durability (service life reaches 100 years), mechanical strength, low thermal conductivity.
The foam glass does not burn even at record high temperatures, only melting of the material is possible without the release of dangerous toxins. The material is moisture resistant, but rather heavy, overall, so the optimal place to use it is the basement.
Fibrous
Externally, the material resembles cotton wool, since it consists of chaotically located finest white or milky fibers. Such insulation is called - "cotton wool." Form release - rolls or mats.
Mineral wool is also sheet. Sheet products have a lower stiffness compared to their counterparts in mats. If we talk about fire-resistant fiber insulation, then they include several types.
- Glass wool. Maintains heating to 500 ° C, keeping the technical characteristics. These include heat efficiency, durability, low weight. However, the material is prone to shrinkage, and during work it requires special protection, since thin fibers prick, stick under the skin, and the smallest particles irritate the mucous membranes of the upper respiratory tract.
- Basalt wool. Basalt wool is based on fibers from rocks that are previously exposed to heat above 1300 ° C. This is due to the ability of wool to withstand high temperatures, up to 1000 ° C.Today stone wool is one of the best thermal insulation materials: it has a low moisture absorption coefficient, is vapor permeable, does not shrink, is environmentally friendly and biostable.
- Ecowool 80% consists of recycled cellulose, which has been a special flame retardant treatment. The material is environmentally friendly, has a low weight and low coefficient of insulation, but a small moisture resistance.
Liquid
Raw materials are sprayed with the use of special equipment, after solidification forms a mass, in appearance and to the touch resembling expanded polystyrene. The most known type of liquid fire-resistant heaters is liquid polyurethane.
It is characterized by environmental safety, and thanks to the method of application and improved adhesive properties, it is evenly distributed over the surface, filling cracks and joints. This, firstly, ensures the durability of thermal insulation, and, secondly, guarantees its quality and the absence of “cold bridges”.
Criterias of choice
- Achieve high heat efficiency It is possible, choosing a heater with a low coefficient of thermal conductivity.In addition, we must not forget that when the room is insulated, only 20-25% of heat losses occur on walls. In this regard, to approach the issue of insulation should be a complex, the maximum effect can be achieved only by creating a completely sealed design.
- An important criterion is the cost of the product. It should be remembered that high-quality insulation can not be cheap. Unjustified price reduction means a violation of insulation technology, which directly affects its technical features.
- With the purchase of modern mineral wool insulation pay attention to the location of the fibers. Preference should be given to products with a chaotic arrangement. Unlike analogues with horizontally or vertically oriented fibers, they are characterized by higher thermal and acoustic insulation.
- Fireproof facade material, in addition to low thermal conductivity, must demonstrate good water resistance and biostability. The characteristics of environmental safety and the absence of toxic substances in its composition are important for finishing the house inside.
- If the mineral wool insulation is not subjected to stress (for example,placed on the frame or between the bearing structures), you can choose a less dense (up to 90 kg / cubic meter) option. It is cheaper. If the material is under pressure, then indicators of strength and tensile strength and compression become important.
These qualities demonstrate denser (semi-rigid and solid rigid) analogues with higher cost.
Scope of application
Despite the fact that all heaters are used to maintain the desired temperature parameters inside the room or equipment, its different types have different purposes.
The most widespread basalt wool. It is more active than other non-combustible materials used for external insulation of facades. It is noteworthy that wool is equally effective for use as a plaster, and in the system of the hinged facade. It allows you to organize very high-quality ventilated facades.
Mineral wool is also used in the maintenance of these works, but much less. This is due to the worst indicators of water resistance and vapor permeability of the mineral wool, as well as its tendency to shrinkage.
However, possessing greater elasticity, mineral wool is optimal for finishing structures of complex shapes, production units.
For insulation of an unused loftAs well as a layer of floors on the first floors of buildings, it is best to use bulk materials, for example, expanded clay. For rooms characterized by high humidity (baths, saunas, houses located near water), it is important to choose moisture-proof and vapor-insulating insulation. Stone wool is primarily responsible for these requirements.
For insulation of residential premises (floor, walls, ceiling, partitions) basalt wool is mainly used. For warming horizontal surfaces, especially the floor, it is more convenient to use rolled materials, for example, mineral wool. The same material is widely used for thermal insulation of wooden buildings. Mineral-cotton sheets are stacked from the inside of the building between the supporting rafters.
To fill the voids of the wall masonry bulk materials are commonly used. It should be remembered that when heated, claydite begins to release toxic substances, so his choice is not the best option for a bath. More environmentally friendly bulk fillers - exfoliated vermiculite and perlite. The first, however, is extremely susceptible to moisture.Perlite is ideal for filling this kind of voids, as well as for laying roofs of the inclined type.
However, vermiculite has a lower thermal conductivity compared to other bulk materials, and even mineral wool. This allows you to fill it with a thin layer, avoiding excessive load on the bearing elements of the structure.
Bulk insulation materials are also used for mixing in mortars for organizing floor screed and pouring on the ground.
Installation of non-combustible insulation is an obligatory stage of work when organizing a roof with a chimney. In the place where the pipe and its elements pass through the walls and roof, it is necessary to have a fire-resistant insulation that will not allow high temperatures to spread over the surface.
As a rule, basalt (for stainless steel pipes) or mineral wool (for brick chimneys) in the form of slabs is used for these purposes. Such heaters have a greater level of heat capacity, they are tougher and more durable. In addition to sound and heat insulation, the material serves as fireproof insulation. Another insulation for the chimney - foam glass.
For water supply systems, air ducts basalt insulation is also used, which protects pipes from freezing at negative temperatures.
Tips and tricks
- Despite the long service life of foam glass, it should be protected from mechanical damage. Perlite, which is rapidly destroyed even under insignificant loads, which leads to the loss of technical properties, requires a careful attitude.
- If it is necessary to improve the thermal efficiency of mineral wool insulation, and there is no opportunity to lay it with a thick layer, the purchase of basalt wool or glass wool with a foil layer will be an excellent solution.
- Standard rolls and sheets are equipped with a foil layer on one side, which contributes to the reflection of heat rays. This material, in addition to increased thermal insulation properties, is characterized by better resistance to water, higher sound insulation properties.
- To create a solid heat-resistant barrier, the foiled materials are additionally glued with metallized adhesive tape during installation.
- Bulk materials are poured over the vapor barrier film and covered with a waterproof film on top.
Test for fire safety of various heaters, see the following video.